WHAT DOES THE ASSET MANAGEMENT FEATURE IN QMULUS DO?
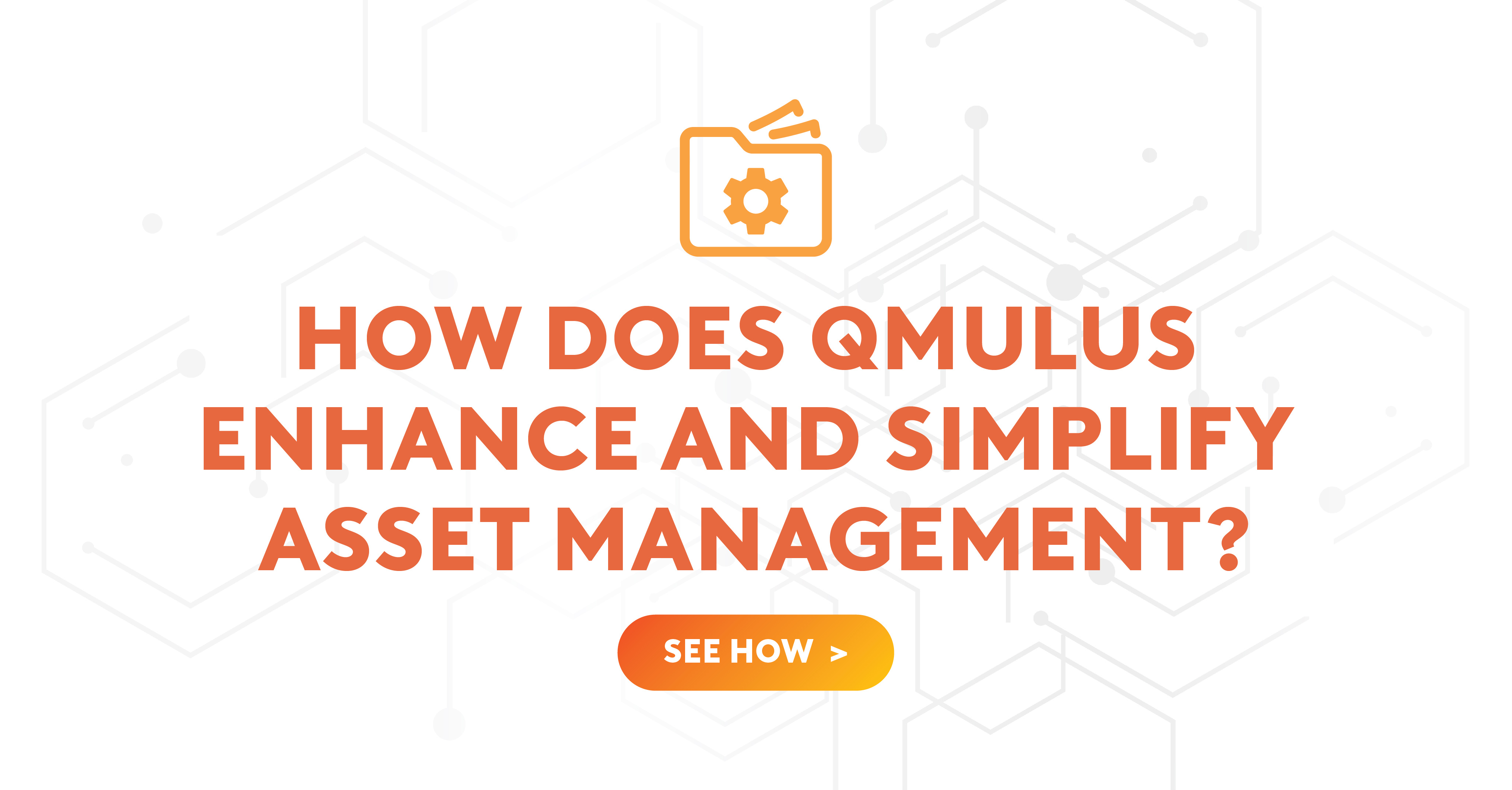
Efficiently managing and maintaining equipment across multiple locations is crucial for any business. The QMULUS Asset Management app bridges data gaps, provides complete visibility, and offers comprehensive maintenance oversight for all your heat treat equipment. It helps you understand the full lifecycle of your assets, providing the critical information you need when you need it. Whether your assets are spread across multiple sites or centralized in one facility, QMULUS empowers you with the data necessary to keep your operations running smoothly. Let’s dive into what QMULUS Asset Management can do for you, especially if you're in engineering, manufacturing, or operations.
Overview of Asset Management
QMULUS Asset Management gives you detailed insights into each piece of equipment, from its components to its part structure. Imagine having all your technical drawings, user manuals, and maintenance instructions in one accessible place. This centralized approach means you can handle maintenance and operational tasks seamlessly, reducing downtime and boosting productivity. It’s like having a well-organized toolbox that helps you get the job done efficiently.
- Equipment Management
Managing your assets with QMULUS is like having a smart system that keeps everything in check across different locations:
- Centralized Asset Overview: You get a clear view of all your assets, whether they’re at specific sites or company-wide. This makes it easy to stay on top of equipment status and details, which is crucial for maintenance and monitoring.
- Efficient Issue Identification: Spot problems early with organized displays and notifications. It’s like having a proactive assistant that alerts you before things go wrong.
- Adding and Updating Equipment: Adding new equipment is a breeze. Just select the location and fill in the details. You can also update existing information to keep everything accurate and up-to-date.
Figure 1: The equipment is organized by company and location. Selecting a location (1) will reveal all associated assets and equipment (2), along with details such as asset ID, process type, status, and notifications.
- Spare Parts Management
Keeping your equipment running smoothly means managing spare parts effectively:
- Inventory Management: Maintain an up-to-date inventory of spare parts to avoid any unexpected downtime.
- Lifecycle Tracking: Know exactly when to replace parts based on their usage and lifecycle stages.
- Detailed Information: Each spare part entry includes specs and compatibility details, ensuring your maintenance teams have the right information at their fingertips.
- Maintenance Planning: Plan preventive maintenance more effectively to extend your equipment’s lifespan.
- Document Management
With QMULUS, document management is a breeze:
- Centralized Storage: Store all your technical documents in one place for easy access.
- Organized Categories: Categorize and filter documents so you can find what you need quickly during maintenance or operations.
- Ease of Access: No more digging through files. Find the right document when you need it most.
- Operational Efficiency: Streamline workflows with organized documents, reducing search time and ensuring everyone has the latest information.
Figure 2 - Document management offers a centralized solution for storing, organizing, and retrieving all documents associated with assets.
- Communication and User Requests
Handling maintenance issues and service requests is simpler with QMULUS:
- Service Requests: Log and track service requests linked to specific assets, ensuring nothing slips through the cracks.
- Centralized Communication: Keep all asset-related communications in one place for better coordination and faster response times.
- Improved Service Quality: Resolve issues promptly with a clear system that keeps everyone in the loop.
Figure 3 – Customer/User requests streamline the maintenance and service process by centralizing and organizing all related communications.
- Sensor Settings
Customizable sensor settings give you precision control over equipment monitoring:
- Naming Conventions: Standardize data across different systems and manufacturers for consistency.
- Visibility and Display: Customize how sensors are displayed and referenced so everyone understands their significance.
- Data Accuracy: Link sensors to their sources for accurate data collection and monitoring integrity.
Figure 4 – Customizable sensor settings provide flexibility and precision by standardizing naming conventions, tailoring visibility and display, and linking sensors to their data sources for accurate monitoring and data interpretation.
- Asset Profile
QMULUS’ asset profiles help you organize information systematically:
- Define Asset Types: Categorize assets with specific details and subcategories for clarity.
- Hierarchical Structure: Visualize asset relationships with a structured tree format.
- Consistency: Ensure all asset information is correctly mapped and retrievable across your system.
Figure 5 – Asset profiles categorize and organize information hierarchically, defining asset types with detailed structures, using a tree format for easy navigation, and ensuring consistent information mapping across similar assets.
Conclusion
QMULUS Asset Management is your go-to solution for efficient equipment management. By integrating essential capabilities like asset oversight, spare parts management, document handling, communication facilitation, sensor customization, and asset profiling, QMULUS ensures your operations run smoothly. Whether you’re in engineering, manufacturing, or production, this tool is designed to boost efficiency, organization, and effectiveness, ultimately improving productivity and extending equipment lifespan.